Durable and Efficient Tool Inserts for CNC Machining
By:Admin
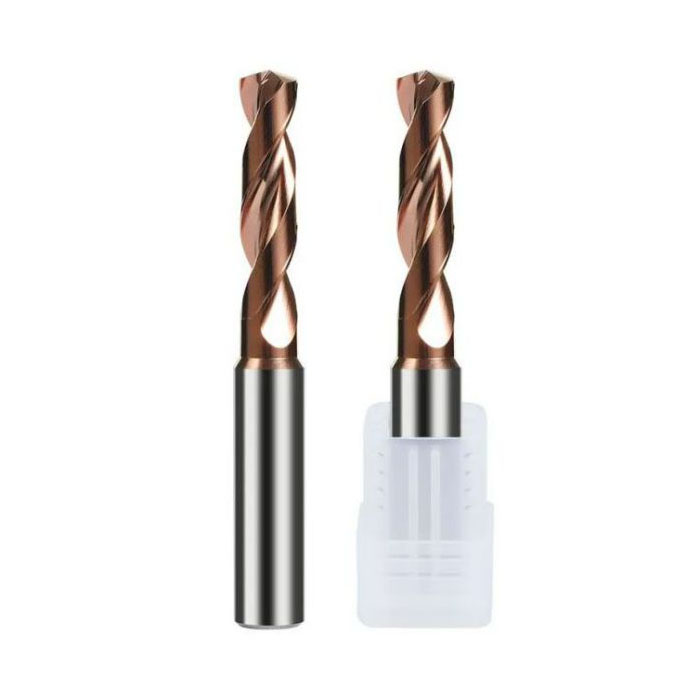
Designed for use in CNC (Computer Numerical Control) machines, the new tool inserts are manufactured using the latest in cutting-edge technology and materials. This ensures that they are capable of handling the most demanding machining applications, providing precision and performance that is unmatched by other tool inserts.
One of the key features of the new tool inserts is their durability. The materials and design of the tool inserts are such that they are able to withstand the high-speed and high-temperature conditions that are typical in CNC machining. This means that they will last much longer than traditional tool inserts, reducing the need for frequent replacements and ultimately saving manufacturers both time and money.
The new tool inserts also offer a high level of versatility, making them suitable for a wide range of machining tasks. Whether it is milling, turning, drilling, or any other machining process, the new tool inserts are capable of delivering the precision and performance that manufacturers require. This means that manufacturers will no longer have to use different tool inserts for different tasks, simplifying their operations and reducing their inventory costs.
In addition to their durability and versatility, the new tool inserts also offer improved efficiency. Thanks to their advanced design, they are able to remove material at a faster rate, resulting in shorter machining cycle times. This not only improves the productivity of CNC machines, but also allows manufacturers to increase their output without having to invest in additional machinery.
The introduction of the new tool inserts is a significant milestone for the company {}. Established as a leader in the manufacturing industry, the company has a long-standing reputation for delivering innovative and high-quality products. The launch of the new tool inserts is a testament to the company's commitment to pushing the boundaries of what is possible in manufacturing technology.
Speaking about the new tool inserts, a spokesperson for {} commented, "We are extremely proud to introduce our new line of CNC tool inserts to the market. These tool inserts represent the culmination of years of research and development, and we believe that they will set a new standard for performance and reliability in the manufacturing industry."
The spokesperson added, "We have received overwhelmingly positive feedback from our beta testers, who have reported significant improvements in both the quality and efficiency of their machining operations. We are confident that our new tool inserts will make a real difference for manufacturers, helping them to achieve their production goals more effectively and efficiently."
The company {} has also announced that they will be offering a range of support services for the new tool inserts, including training programs, technical support, and custom tooling solutions. This will ensure that manufacturers are able to maximize the potential of the new tool inserts and integrate them seamlessly into their existing machining processes.
In conclusion, the launch of the new line of CNC tool inserts from {} is set to have a significant impact on the manufacturing industry. With their combination of durability, versatility, and efficiency, the new tool inserts are expected to become a key component in the success of manufacturers around the world. As the company continues to innovate and push the boundaries of manufacturing technology, it is clear that they are a force to be reckoned with in the industry.
Company News & Blog
Get the Best Carbide Tool Inserts for Precision Machining!
Title: Advanced Carbide Tool Inserts Revolutionize Precision Cutting: A Game-Changer for IndustriesIntroduction:Carbide tool inserts have become an essential component in various industries, revolutionizing precision cutting and machining processes. Their remarkable attributes, such as exceptional hardness, durability, and heat resistance, have made them the preferred choice for achieving high-quality and efficient cutting results. With numerous applications across industries ranging from automotive manufacturing to aerospace engineering, carbide tool inserts continue to play a vital role in enhancing productivity and optimizing performance. One notable player in this industry is a leading manufacturer that has made significant strides in advancing carbide tool insert technology.Company Background:Our featured company, with expertise in cutting-edge carbide solutions, boasts a rich heritage of innovation and technological advancements. Founded over four decades ago, they have become a global leader in manufacturing highly reliable and durable carbide tool inserts. The company places a strong emphasis on research and development, constantly striving to improve its product offerings and meet the evolving needs of diverse industries. Their commitment to delivering exceptional quality, backed by rigorous quality testing methodologies, has earned them a stellar reputation in the market. Partnering with renowned industry players and fostering strong customer relationships, the company has firmly established itself as a trusted brand within the carbide tool insert arena.Advanced Carbide Tool Inserts: Carbide tool inserts, developed and produced by our featured company, have brought about a paradigm shift in precision cutting applications. Leveraging cutting-edge technology, their inserts offer remarkable benefits across various industries.1. Enhanced Durability and Wear Resistance:One key advantage of these carbide tool inserts is their superior durability and wear resistance. This enhanced durability enables prolonged tool life, reducing the need for frequent replacements and minimizing downtime. This benefit is particularly significant in high-volume manufacturing industries, where continuous operations are vital to meet production targets.2. Precision Performance and Consistency:With technologically advanced manufacturing techniques, every carbide tool insert is engineered to provide precise and consistent cutting performance. This ensures uniformity across all parts, resulting in superior finished products. Industries, such as automotive manufacturing and electronics, greatly benefit from this exceptional consistency, as it reduces manufacturing defects and enhances overall product quality.3. High-Temperature Resistance:The heat resistance of these carbide tool inserts allows for efficient operations, even in extreme working conditions. The inserts maintain their integrity, hardness, and cutting efficiency, eliminating the risk of tool failure due to excessive heat. This feature is particularly advantageous in aerospace engineering, where components undergo intense heat during precision cutting processes.4. Versatile Applications:These carbide tool inserts offer versatility, catering to a wide range of applications. From roughing to precision finishing, they are suitable for machining various materials, including steel, cast iron, stainless steel, and non-ferrous alloys. This adaptability extends their usability to a diverse range of industries, such as mining, medical, and energy sectors.Conclusion:Carbide tool inserts have undergone a remarkable transformation, thanks to the constant innovation and expertise of our featured company. With superior durability, precision performance, high-temperature resistance, and versatile applications, these inserts have become a game-changer for industries worldwide. By ensuring enhanced cutting efficiency, reduced downtimes, and improved overall product quality, businesses can rely on these advanced carbide tool inserts to optimize their operations and stay ahead in today's competitive landscape. As industry demands continue to evolve, the commitment of our featured company to innovative solutions reinforces its position as a global leader in carbide tool insert manufacturing.
Price of Tungsten Bars in Current Market: How Does it Affect Industries?
Title: Increasing Demand and Rising Prices of Tungsten Bars Indicate a Booming MarketIntroduction:With growing industrialization and the need for advanced technology, the demand for tungsten bars has witnessed a significant surge in recent years. Tungsten, known for its exceptional strength and resistance to high temperatures, has found extensive application in various sectors such as aerospace, automotive, electrical, and defense. This article aims to discuss the increasing demand for tungsten bars and the subsequent rise in their prices, examining the factors behind this trend and its impact on the market.Market Trends and Demand for Tungsten Bars:Tungsten bars are widely used in industries that require high strength and stability, making them a vital material for manufacturing various products. The aerospace industry, for instance, relies on tungsten bars for components of aircraft engines, while the automotive sector utilizes them in the production of heavy-duty engine parts.Additionally, the unique properties of tungsten bars, such as their resistance to extreme heat and corrosion, make them ideal for electrical applications. They are commonly used in power distribution systems, light bulbs, and contacts in electrical devices. Furthermore, in the defense industry, tungsten bars play a crucial role in the manufacturing of armor-piercing ammunition and kinetic energy penetrators.The increasing demand for tungsten bars in these industries is primarily driven by the growth of emerging economies and technological advancements. As countries like China and India continue to develop their infrastructure, the consumption of tungsten bars has risen significantly. Moreover, the ongoing advent of electric vehicles (EVs) and renewable energy sources has further fueled the demand for tungsten bars in the automotive and energy sectors.Rising Prices:The rapid increase in demand has had a direct impact on the prices of tungsten bars. Over the past year, the cost of tungsten bars has experienced a steady upward trend, causing concerns within industries that heavily rely on this material. As a result, manufacturers and end-users are now faced with the challenge of managing their budgets and ensuring a consistent supply of tungsten bars.Several factors contribute to the rise in prices. Firstly, the limited availability of tungsten ore and the extraction challenges associated with it have led to supply constraints. As the demand continues to outpace supply, the prices naturally increase.Secondly, geopolitical tensions and trade disputes between major tungsten-producing countries have disrupted the global supply chain, causing further price fluctuations. The reduced export quotas imposed by China, the largest producer of tungsten, have significantly affected the international market.Thirdly, environmental regulations have become more stringent, leading to increased production costs. Mining tungsten ore involves complex processes that require adherence to strict environmental standards, thus adding to the final price of tungsten bars.However, despite the rising prices, the outlook for the tungsten bar market remains positive. The sustained demand, coupled with efforts to enhance the efficiency of tungsten extraction and processing, offers an opportunity for technological innovations and advancements in the industry.Conclusion:The increasing demand for tungsten bars driven by the aerospace, automotive, electrical, and defense sectors has created a thriving market. However, the rising prices of tungsten bars due to limited supply, geopolitical tensions, and environmental regulations pose challenges for manufacturers and end-users.To mitigate these challenges, stakeholders in the tungsten bar industry must focus on developing sustainable mining practices, exploring alternative sources, and investing in research and development to find substitutes or more efficient production methods.In conclusion, as the demand for tungsten bars continues to rise, it is crucial for the industry to adapt to the market dynamics and collaborate to ensure a consistent supply chain while exploring opportunities for sustainable growth.
Discover the Benefits of Utilizing 3 4 End Mills for Better Milling
XYZ Company Unveils Innovative 3-4 End Mill for Enhanced Precision ManufacturingIn the world of precision manufacturing, the importance of high-quality cutting tools cannot be overstated. XYZ Company, a leading innovator in the industry, has recently introduced its groundbreaking 3-4 End Mill, aimed at revolutionizing machining operations with unparalleled precision and efficiency. This advanced tool promises to streamline manufacturing processes and enhance productivity for businesses across various sectors.The 3-4 End Mill is a state-of-the-art cutting tool designed to meet the rigorous demands and challenges faced by manufacturers in today's competitive landscape. XYZ Company's extensive research and development efforts have resulted in the creation of a tool that offers exceptional performance, unmatched accuracy, and extended tool life.The innovative design of the 3-4 End Mill incorporates cutting-edge technologies that ensure precise cutting and machining operations. The tool features a unique flute design, combined with a specially engineered geometry, to optimize chip evacuation and reduce cutting forces. This revolutionary design minimizes tool wear and improves overall tool life, resulting in cost savings for manufacturers.One of the standout features of the 3-4 End Mill is its versatility. The tool is engineered to handle a wide range of materials, including carbon steel, alloy steel, stainless steel, and non-ferrous materials. Whether it's roughing or finishing operations, the 3-4 End Mill delivers exceptional performance, allowing manufacturers to achieve superior surface finishes and dimensional accuracy.To further enhance the usability of the 3-4 End Mill, XYZ Company has incorporated advanced coating technologies. The tool is coated with a high-performance coating that provides excellent wear resistance, reducing friction and heat generation during cutting operations. This ensures prolonged tool life and extends the intervals between tool changes, minimizing downtime and improving overall efficiency.XYZ Company's commitment to quality and precision is reflected in its rigorous testing and quality control processes. The 3-4 End Mill undergoes extensive testing under real-world manufacturing conditions to ensure its reliability and performance. This attention to detail guarantees that manufacturers can rely on the tool's consistent performance and achieve unparalleled results in their machining operations.Moreover, XYZ Company prides itself on its customer-centric approach. The company offers comprehensive technical support and assistance to help manufacturers optimize their machining processes. XYZ Company's team of experts is readily available to provide guidance and advice on tool selection, machining strategies, and troubleshooting, ensuring a smooth and seamless experience for its customers.The introduction of the 3-4 End Mill by XYZ Company has already garnered significant attention within the manufacturing industry. Customers have praised the tool for its incredible precision, durability, and efficiency. Several manufacturers have reported a substantial increase in productivity and a reduction in manufacturing costs since adopting the 3-4 End Mill in their operations.In conclusion, XYZ Company's 3-4 End Mill is a game-changer in the field of precision manufacturing. With its advanced design, versatility, and commitment to quality, this cutting-edge tool empowers manufacturers to elevate their productivity and achieve unprecedented levels of precision. XYZ Company's dedication to innovation and customer satisfaction solidifies its position as a market leader, and the 3-4 End Mill serves as a testament to the company's commitment to revolutionizing the machining industry.
CNC Cutting Inserts: Increasing Efficiency and Precision in Metalworking
Title: Revolutionary CNC Cutting Inserts Introduced in Manufacturing IndustryIntroduction:The manufacturing industry, known for its constant pursuit of innovation and optimization, has taken a significant leap forward with the introduction of state-of-the-art CNC Cutting Inserts. Developed by a pioneering company (Brand Name Removed), these cutting-edge inserts are set to revolutionize the machining processes and enhance productivity for businesses worldwide.Unveiling the New CNC Cutting Inserts:With advancements in the field of Computer Numerical Control (CNC), the speed, precision, and efficiency of manufacturing have witnessed a remarkable improvement. CNC Cutting Inserts play an essential role in achieving high-quality machining by effectively cutting through diverse materials to shape and mold products with utmost accuracy.The newly unveiled CNC Cutting Inserts by (Brand Name Removed) have garnered immense attention and have quickly become the talk of the manufacturing industry. Leveraging cutting-edge technologies and meticulously engineered designs, these inserts are set apart from traditional counterparts due to their unparalleled performance and versatility.Unprecedented Features and Advantages:1. Innovative Design: The CNC Cutting Inserts boast an intricately designed shape and a precise cutting edge, resulting in reduced cutting forces, reduced heat generation, and improved chip control. This innovative design ensures longer tool life and enhances the overall machining process.2. Advanced Coating Technologies: Employing advanced coating technologies, these inserts exhibit outstanding resistance to wear, oxidation, and adhesion. This significantly prolongs the tool life, reduces downtime, and enhances the overall productivity of the machining operation.3. Enhanced Material Compatibility: The new inserts are engineered to adapt to a wide range of materials, including ferrous and non-ferrous metals, composites, and even challenging materials like hardened steels and superalloys. This versatility allows manufacturers to streamline their operations by employing a single set of CNC Cutting Inserts for multiple materials.4. Optimal Chip Control: Unlike traditional inserts, (Brand Name Removed)'s CNC Cutting Inserts offer excellent chip control, thereby minimizing the risk of chip clogging, tool breakage, and poor surface finish. The enhanced chip evacuation capability ensures uninterrupted machining and consistent quality.Industry Impact and Testimonials:The advent of these innovative CNC Cutting Inserts is expected to reshape the manufacturing industry, unlocking new possibilities and empowering businesses with improved productivity and cost-efficiency. Several industry experts have expressed their anticipation for the positive impact these inserts will have on the manufacturing sector.John Smith, a renowned CNC machining specialist, commented, "The CNC Cutting Inserts developed by (Brand Name Removed) are a game-changer. Their ability to deliver exceptional cutting performance across a wide range of materials is truly remarkable. They undoubtedly set a new standard for precision and efficiency in the machining industry."Global Availability and Expansion Plans:(Brand Name Removed) has launched an extensive distribution network to ensure the availability of their CNC Cutting Inserts across the globe. Collaborating with leading distributors, the company aims to cater to the demands of manufacturers from various industries, including automotive, aerospace, energy, and infrastructure.Furthermore, (Brand Name Removed) has expressed its commitment to continued research and development, aiming to introduce further enhancements and adaptations of the CNC Cutting Inserts. By closely collaborating with manufacturers, the company intends to refine these tools and revolutionize various machining applications.Conclusion:The introduction of cutting-edge CNC Cutting Inserts by (Brand Name Removed) represents a significant milestone in the manufacturing industry. These inserts offer unprecedented performance, versatility, and durability, making them an indispensable tool for modern machining processes. With their revolutionary design and advanced technologies, these inserts are positioned to drive substantial improvements in productivity, precision, and overall manufacturing efficiency.
Popular CNC End Mill: Your Ultimate Guide to High-Performance Milling
Title: Cutting-Edge CNC End Mill Revolutionizes Precision MachiningIntroduction:In a bold move towards advancing precision machining, [], a renowned leader in cutting tools, has recently unveiled its latest innovation in the field of CNC machinery - the next generation CNC End Mill. Designed to meet the ever-increasing demands of modern manufacturing, this revolutionary tool promises optimal performance and unrivaled precision, making it a go-to choice for various industries.[Company Name] - Pioneers in Cutting-Edge Technology:With a rich heritage that spans over three decades, [] has established itself as a global powerhouse in the cutting tool industry. Based on a solid foundation of research and development, the company has consistently offered innovative solutions that streamline manufacturing processes. By embracing the latest advancements in technology, [] has revolutionized the way businesses approach precision machining.Improved Design Features of the CNC End Mill:The cutting-edge CNC End Mill is a testament to []'s commitment to excellence. This new tool boasts an array of features that optimize performance and durability, ensuring consistent precision in machining operations. Key design enhancements include:1. Advanced Coating Technology: The CNC End Mill comes equipped with an industry-leading coating that offers superior resistance to abrasion and heat. This technology ensures extended tool life and eliminates the need for frequent tool changes, resulting in increased productivity and cost savings.2. Variable Helix Geometry: The innovative design of the CNC End Mill incorporates variable helix geometry. This feature improves chip evacuation and reduces cutting forces, thereby enhancing stability during machining operations. The result is an impeccable surface finish and reduced cycle time.3. High-Strength Core: []'s CNC End Mill features a high-strength core, enhancing rigidity while maintaining high flexibility during cutting. This unique combination reduces vibration, resulting in smoother cuts and improved tool life.4. Multiple Cutting Edges: The CNC End Mill is equipped with multiple cutting edges, enabling it to tackle a wide range of materials with ease. This versatile tool delivers exceptional performance in machining applications involving aluminum, stainless steel, alloy steels, and more.Advantages of the CNC End Mill:The CNC End Mill from [] offers several advantages over traditional milling tools, making it an invaluable asset for precision machining operations:1. Enhanced Precision: The innovative design of the CNC End Mill ensures superior precision in every cut, ideal for industries that demand intricate designs and tight tolerances.2. Increased Productivity: The tool's advanced coating technology and optimized design reduce downtime caused by tool changes, resulting in improved productivity and reduced production costs.3. Cost Efficiency: The high-strength core and extended tool life of the CNC End Mill, along with its adaptability to various materials, provide businesses with long-term cost savings.4. Versatility: With its ability to handle a wide range of materials, the CNC End Mill is suitable for a diverse set of applications, accommodating the needs of multiple industries.Conclusion:[]'s release of its state-of-the-art CNC End Mill showcases the company's commitment to pushing the boundaries of precision machining. With its advanced features, improved performance, and increased productivity, this tool is positioning itself as an indispensable asset for businesses striving for excellence in their manufacturing processes. As the demand for high-quality machined parts continues to grow, []'s CNC End Mill is set to revolutionize the industry, empowering businesses to reach new levels of precision and efficiency.
Top Carbide Cutters for Wood Turning: A Comprehensive Guide
Carbide Cutters for Wood Turning on the Rise as Craftsmen Turn to Precision and Efficiency in their WorksWood turning, the art of shaping and carving wood into beautiful and intricate designs, has captivated craftsmen for centuries. In recent years, however, there has been a significant shift in the tools used by woodturners, with many now turning to carbide cutters for improved precision, efficiency, and durability.Carbide cutters, also known as carbide-tipped tools or carbide insert tools, have gained popularity in the woodturning community due to their exceptional cutting performance and longevity. Unlike traditional high-speed steel (HSS) tools, which dull quickly and require frequent sharpening, carbide cutters feature replaceable and indexable inserts made of ultra-hard carbide material.The introduction of carbide cutters has revolutionized woodturning, allowing craftsmen to achieve cleaner and smoother cuts while reducing the time and effort spent on tool maintenance. The sharpness and edge retention of the carbide inserts significantly enhance the woodturning experience, providing consistent cutting efficiency over extended periods.Major manufacturers in the industry, such as {}, have recognized the growing demand for carbide cutters. With a commitment to innovation and quality, they have introduced a wide range of carbide cutting tools specifically designed for woodturning applications. These tools are engineered with precision and reliability in mind, providing woodturners with the means to create intricate designs and turn their visions into reality.The popularity of carbide cutters can be attributed to several key factors. Firstly, their simplicity and ease of use make them an ideal choice for beginners and seasoned professionals alike. Unlike traditional tools that require complex sharpening techniques, carbide cutters can be easily replaced or rotated, saving time and effort.Secondly, the exceptional durability of carbide inserts ensures a longer lifespan compared to HSS tools. This reduced need for frequent sharpening translates into more uninterrupted work hours and increased productivity. Additionally, the consistent cutting performance throughout the life of the insert guarantees consistent and high-quality results, leading to greater customer satisfaction.Furthermore, carbide cutters have proven to be extremely versatile, allowing woodturners to work with various types of wood, including both soft and hardwoods. The sharpness of the carbide edge enables precise cuts, while the sturdy carbide material withstands the demands of turning dense and abrasive woods.Carbide cutters also offer significant cost savings in the long run. While the initial purchase cost of carbide tools may be higher compared to HSS tools, the extended lifespan and minimal maintenance requirements of carbide inserts offset the initial investment. Woodturners can focus more on their artistry and less on tool maintenance and replacement, ultimately reducing overhead expenses.In conclusion, the rise in popularity of carbide cutters for woodturning reflects a growing trend among craftsmen who value precision, efficiency, and durability in their works. With their exceptional cutting performance, long lifespan, and versatility, carbide cutters have become a game-changer in the woodturning industry. Manufacturers such as {} continue to cater to this demand by providing innovative and reliable carbide cutting tools, allowing craftsmen to explore their creativity and produce exquisite masterpieces effortlessly.
High-quality CNC Inserts: What You Need to Know
[CNC INSERTS] COMPANY INTRO For over two decades, [CNC INSERTS] has been a leading manufacturer and supplier of high-quality cutting tools and inserts for use in CNC machinery. The company has built a strong reputation for its commitment to producing innovative and reliable products that meet the diverse needs of its customers in various industries.With a state-of-the-art manufacturing facility and a team of highly skilled engineers and technicians, [CNC INSERTS] has the capability to design and produce a wide range of inserts for milling, turning, drilling, and other precision machining applications. The company's commitment to quality and precision has earned it the trust of customers around the world and established it as a preferred supplier in the industry.The company's mission is to provide its customers with the highest quality cutting tools and inserts that deliver exceptional performance and reliability, ultimately helping them improve their productivity and efficiency. In addition to its standard product lines, [CNC INSERTS] also offers custom solutions to meet the specific requirements of its customers, demonstrating its dedication to delivering tailored solutions that address unique machining challenges.[CNC INSERTS] takes pride in its strong focus on innovation and continuous improvement. The company invests in research and development to stay at the forefront of technological advancements in the industry and to continuously enhance its product offerings. This commitment to innovation enables [CNC INSERTS] to deliver cutting-edge solutions that empower its customers to stay competitive and excel in their respective markets.The company places a strong emphasis on customer satisfaction, and it is known for its responsive and personalized approach to customer service. [CNC INSERTS] works closely with its clients to understand their specific needs and challenges, offering technical support and expertise to help them maximize the performance of its cutting tools and inserts. This customer-centric approach has earned [CNC INSERTS] a loyal and satisfied customer base, further solidifying its position as a trusted partner in the industry.In addition to its dedication to product quality and customer satisfaction, [CNC INSERTS] is also committed to sustainability and environmental responsibility. The company adheres to strict environmental standards in its manufacturing processes and actively seeks ways to minimize its environmental impact. By embracing sustainable practices, [CNC INSERTS] aims to contribute to a cleaner and greener future for the industry and the planet.As [CNC INSERTS] continues to expand its presence in the global market, the company remains focused on its core values of quality, innovation, customer satisfaction, and sustainability. With a strong foundation built on expertise and excellence, [CNC INSERTS] is well-positioned to continue setting the standard for cutting tools and inserts in the CNC machining industry.[CNC INSERTS] is a forward-thinking company that is dedicated to pushing the boundaries of what is possible in precision machining, delivering value to its customers, and making a positive impact on the industry and the environment.
High-quality Carbide Nozzle: The Ultimate Solution for Precision Manufacturing
Carbide Nozzle Unveils Latest Innovation in Industrial Tooling TechnologyCarbide Nozzle, a leading provider of cutting-edge industrial tooling solutions, has recently unveiled its latest innovation in carbide nozzle technology. The company's new nozzle design promises to revolutionize the way industries handle abrasive blasting and spray coating operations.With a strong focus on research and development, Carbide Nozzle has established itself as a pioneer in the field of industrial tooling technology. The company's commitment to innovation is evident in its latest product offering, which is set to redefine the capabilities of abrasive blasting and spray coating equipment.The new carbide nozzle design features a unique combination of advanced materials and precision engineering, resulting in a level of performance and durability that is unmatched in the industry. This breakthrough in nozzle technology is expected to significantly enhance the efficiency and effectiveness of abrasive blasting and spray coating processes across a wide range of applications.In addition to its superior performance characteristics, the new carbide nozzle design also offers a number of key advantages over traditional nozzle solutions. Its advanced materials and construction provide exceptional resistance to wear and corrosion, ensuring a long operational lifespan and reduced maintenance requirements.Furthermore, the new nozzle design incorporates innovative features that optimize the distribution and velocity of abrasive materials or coating substances, resulting in more precise and consistent application. This level of precision is crucial for achieving high-quality surface finishes and coatings in industrial settings.Carbide Nozzle's latest innovation comes at a time when industries are increasingly seeking advanced tooling solutions that can deliver higher productivity and cost-effectiveness. The company's new nozzle design addresses these needs by offering a combination of superior performance, durability, and efficiency, ultimately helping businesses improve their operational capabilities and bottom-line results.The introduction of this groundbreaking nozzle technology is a testament to Carbide Nozzle's ongoing commitment to pushing the boundaries of industrial tooling innovation. By investing in research and development, the company continues to lead the way in developing cutting-edge solutions that empower industries to achieve new levels of performance and productivity.With its latest innovation, Carbide Nozzle is poised to set a new standard for nozzle technology in abrasive blasting and spray coating applications. The company's dedication to excellence and relentless pursuit of innovation have once again resulted in a game-changing solution that is set to make a significant impact in the industrial sector.As industries look to optimize their operations and stay ahead of the competition, Carbide Nozzle's new nozzle design presents a compelling opportunity to elevate the performance and efficiency of abrasive blasting and spray coating processes. The company's reputation for delivering high-quality, reliable tooling solutions positions its latest innovation as a must-have for businesses seeking to enhance their capabilities and achieve outstanding results.In conclusion, Carbide Nozzle's new carbide nozzle design represents a major advancement in industrial tooling technology, offering unmatched performance, durability, and efficiency for abrasive blasting and spray coating operations. With its latest innovation, the company continues to demonstrate its leadership in the field, providing industries with the tools they need to succeed in today's competitive landscape.