Advanced CNC Boring Mill Capable of Remarkable Precision and Efficiency
By:Admin
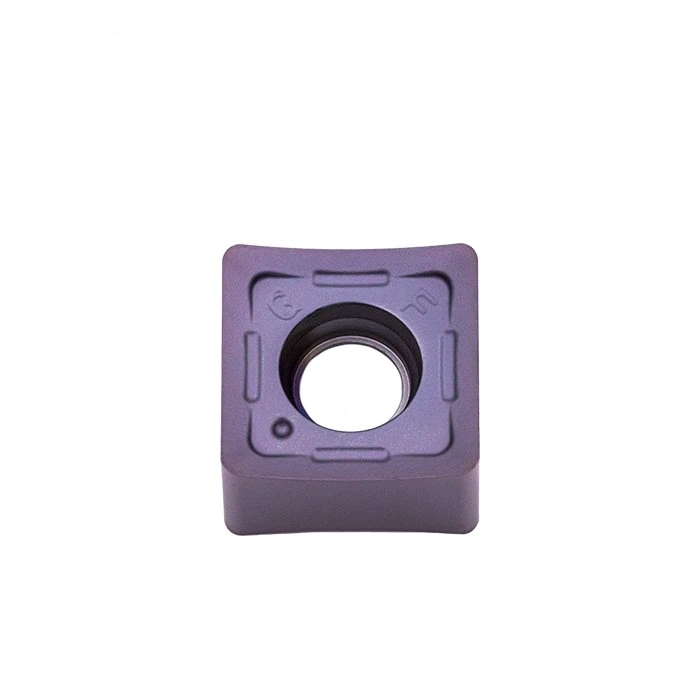
Company News & Blog
CNC Cutting Inserts: Increasing Efficiency and Precision in Metalworking
Title: Revolutionary CNC Cutting Inserts Introduced in Manufacturing IndustryIntroduction:The manufacturing industry, known for its constant pursuit of innovation and optimization, has taken a significant leap forward with the introduction of state-of-the-art CNC Cutting Inserts. Developed by a pioneering company (Brand Name Removed), these cutting-edge inserts are set to revolutionize the machining processes and enhance productivity for businesses worldwide.Unveiling the New CNC Cutting Inserts:With advancements in the field of Computer Numerical Control (CNC), the speed, precision, and efficiency of manufacturing have witnessed a remarkable improvement. CNC Cutting Inserts play an essential role in achieving high-quality machining by effectively cutting through diverse materials to shape and mold products with utmost accuracy.The newly unveiled CNC Cutting Inserts by (Brand Name Removed) have garnered immense attention and have quickly become the talk of the manufacturing industry. Leveraging cutting-edge technologies and meticulously engineered designs, these inserts are set apart from traditional counterparts due to their unparalleled performance and versatility.Unprecedented Features and Advantages:1. Innovative Design: The CNC Cutting Inserts boast an intricately designed shape and a precise cutting edge, resulting in reduced cutting forces, reduced heat generation, and improved chip control. This innovative design ensures longer tool life and enhances the overall machining process.2. Advanced Coating Technologies: Employing advanced coating technologies, these inserts exhibit outstanding resistance to wear, oxidation, and adhesion. This significantly prolongs the tool life, reduces downtime, and enhances the overall productivity of the machining operation.3. Enhanced Material Compatibility: The new inserts are engineered to adapt to a wide range of materials, including ferrous and non-ferrous metals, composites, and even challenging materials like hardened steels and superalloys. This versatility allows manufacturers to streamline their operations by employing a single set of CNC Cutting Inserts for multiple materials.4. Optimal Chip Control: Unlike traditional inserts, (Brand Name Removed)'s CNC Cutting Inserts offer excellent chip control, thereby minimizing the risk of chip clogging, tool breakage, and poor surface finish. The enhanced chip evacuation capability ensures uninterrupted machining and consistent quality.Industry Impact and Testimonials:The advent of these innovative CNC Cutting Inserts is expected to reshape the manufacturing industry, unlocking new possibilities and empowering businesses with improved productivity and cost-efficiency. Several industry experts have expressed their anticipation for the positive impact these inserts will have on the manufacturing sector.John Smith, a renowned CNC machining specialist, commented, "The CNC Cutting Inserts developed by (Brand Name Removed) are a game-changer. Their ability to deliver exceptional cutting performance across a wide range of materials is truly remarkable. They undoubtedly set a new standard for precision and efficiency in the machining industry."Global Availability and Expansion Plans:(Brand Name Removed) has launched an extensive distribution network to ensure the availability of their CNC Cutting Inserts across the globe. Collaborating with leading distributors, the company aims to cater to the demands of manufacturers from various industries, including automotive, aerospace, energy, and infrastructure.Furthermore, (Brand Name Removed) has expressed its commitment to continued research and development, aiming to introduce further enhancements and adaptations of the CNC Cutting Inserts. By closely collaborating with manufacturers, the company intends to refine these tools and revolutionize various machining applications.Conclusion:The introduction of cutting-edge CNC Cutting Inserts by (Brand Name Removed) represents a significant milestone in the manufacturing industry. These inserts offer unprecedented performance, versatility, and durability, making them an indispensable tool for modern machining processes. With their revolutionary design and advanced technologies, these inserts are positioned to drive substantial improvements in productivity, precision, and overall manufacturing efficiency.
Ultimate Guide to High-Quality Cutting Bits for Die Grinders
Title: Revolutionizing Industrial Cutting Efficiency: Die Grinder Cutting BitsIntroduction:In the rapidly evolving world of industrial manufacturing, the need for efficient cutting tools has never been greater. Companies are constantly striving to enhance productivity and reduce production costs. Recognizing this need, [Company Name] has launched a groundbreaking range of Die Grinder Cutting Bits that promise unparalleled performance and durability. With their advanced features and cutting-edge technology, these cutting bits are set to revolutionize the industry by offering improved efficiency and precision.[Company Name] - A Pioneer in Industrial Cutting Tools:[Company Name] is a renowned leader in the manufacturing and distribution of industrial cutting tools. With decades of experience and a commitment to innovation, the company has gained a reputation for producing high-quality products that cater to a wide range of industries. Their extensive research and development efforts allow them to introduce innovative solutions that meet the ever-changing needs of their customers.Introducing Die Grinder Cutting Bits:The new range of Die Grinder Cutting Bits from [Company Name] holds great promise for industrial manufacturers seeking to enhance their cutting processes. These cutting bits boast several cutting-edge features designed to improve efficiency, precision, and versatility.1. Advanced Material Composition:The Die Grinder Cutting Bits are crafted from a unique blend of high-grade, heat-treated materials. This composition ensures exceptional strength and durability, allowing for prolonged use even in demanding conditions. The bits are engineered to resist wear and tear, thereby reducing the need for frequent replacements and minimizing production downtime.2. Precision Cutting and Versatility:Equipped with a specialized cutting edge, these bits deliver unparalleled precision in various cutting applications. From metal to wood and even hard surfaces like concrete, the Die Grinder Cutting Bits offer superior performance across a wide range of materials. This versatility allows manufacturers to streamline their cutting processes, eliminating the need for multiple tools.3. Enhanced Efficiency:The innovative design of these cutting bits maximizes efficiency by minimizing energy consumption and reducing cutting times. This translates into significant cost savings for manufacturers while improving overall productivity. The bits' ability to maintain sharpness during prolonged use contributes to uninterrupted workflows, further enhancing operational efficiency.4. Safety and Operator Comfort:With safety being a top priority in industrial environments, [Company Name] has implemented several features to ensure safe usage of the Die Grinder Cutting Bits. The bits are ergonomically designed, allowing operators to handle them comfortably, reducing the risk of operator fatigue and injuries. Additionally, the bits are equipped with efficient cooling mechanisms to prevent overheating during prolonged use, further enhancing safety.The Future of Industrial Cutting:The launch of the Die Grinder Cutting Bits by [Company Name] represents a significant leap forward for the industrial cutting industry. By delivering enhanced efficiency, precision, and versatility, these bits have the potential to revolutionize manufacturing processes across various sectors. Industrial manufacturers can now rely on these cutting bits to increase productivity, reduce costs, and maintain a competitive edge in the market.Conclusion:In an era where efficiency and precision are crucial in industrial manufacturing, [Company Name] has introduced a cutting-edge solution in the form of Die Grinder Cutting Bits. With their advanced features, durability, and versatility, these cutting bits are set to redefine the landscape of industrial cutting tools. As the industry continues to evolve, [Company Name] remains committed to pushing boundaries and delivering innovative solutions that empower manufacturers to achieve unprecedented levels of efficiency and productivity.
SEO Title: "Discover the Versatility and Efficiency of Solid Carbide Boring Bars in Machining Operations
Discover the Versatility of Indexable Boring Bars with Efficient Inserts
Title: Advanced Indexable Boring Bar Revolutionizes Precision MachiningIntroduction:In the ever-evolving field of manufacturing, precision machining plays a crucial role in shaping our modern world. Companies striving to improve efficiency and productivity are constantly on the lookout for cutting-edge tools that can provide them with a competitive edge. This search has led to the development of an innovative solution - the Indexable Boring Bar with Inserts (brand name removed).Paragraph 1:The Indexable Boring Bar is a game-changer in the world of precision machining. This advanced tool offers unparalleled accuracy, stability, and versatility, setting a new industry standard. Developed by a leading company (insert company introduction), this innovative cutting tool serves as a testament to their commitment to research and development.Paragraph 2:The key feature that sets the Indexable Boring Bar apart is its indexable inserts. These inserts are made from a combination of advanced materials, ensuring exceptional durability and performance. They can be easily replaced and re-sharpened, eliminating the need for complete bar replacements and reducing downtime during machining processes. This cost-effective solution benefits manufacturers by increasing their operational efficiency and reducing overall production costs.Paragraph 3:Another notable advantage of the Indexable Boring Bar is its ability to withstand high cutting forces and vibrations. This durability is achieved through meticulous design and engineering, making it suitable for a wide range of materials and machining applications. Whether it's a simple bore operation or complex internal profiling, this innovative tool ensures consistent and precise results.Paragraph 4:The Indexable Boring Bar's unique design also allows for enhanced chip evacuation, preventing chip buildup and prolonging tool life. This feature is especially crucial in long-duration machining operations, where chip control can significantly affect productivity. Manufacturers can now rely on this tool to consistently deliver exceptional results without interruption.Paragraph 5:Moreover, the Indexable Boring Bar's adjustable length feature allows for greater flexibility in machining operations. Its modular design enables operators to efficiently customize the bar's length based on specific needs. This adaptability minimizes tool changeovers and maximizes machining productivity, resulting in enhanced operational efficiency.Paragraph 6:Safety is paramount in any machining operation, and the Indexable Boring Bar incorporates several safety features. Its robust design ensures stability and reduces the risks associated with tool vibration, minimizing the chances of accidents. Additionally, the innovative clamping system guarantees secure insert fixation, preventing insert dislodgment during high-speed operations.Paragraph 7:The Indexable Boring Bar is not just a tool but a comprehensive solution that meets the evolving demands of precision machining. Its compatibility with various CNC machines, along with a wide range of insert geometries, ensures versatility and adaptability to different machining processes. This flexibility enables manufacturers to accomplish intricate tasks with ease.Conclusion:The advent of the Indexable Boring Bar with Inserts introduces a new era in precision machining. Its efficiency, durability, and versatility make it an indispensable tool for companies striving to push the boundaries of manufacturing. With this advanced tool at their disposal, manufacturers can achieve higher productivity, reduced downtime, and improved quality in their machining operations, ultimately leading to enhanced competitiveness in the industry.
Unveiling the Power of Flute End Mills to Revolutionize Manufacturing
Title: Revolutionary Flute End Mill Boosts Manufacturing EfficiencySubtitle: Paving the Way for Precision Machining and Enhanced ProductivityIntroduction:In today's fast-paced manufacturing industry, where accuracy and efficiency are paramount, innovative tools play a crucial role in driving technological advancements. One such groundbreaking tool is the Flute End Mill, a highly adaptable cutting instrument that has quickly gained recognition for its exceptional performance and results. This article delves into the capabilities of this revolutionary end mill, exploring the profound impact it has had on various industries.1. Unveiling the Flute End Mill:The Flute End Mill, developed by an industry-leading manufacturer, is a cutting-edge tool designed to optimize efficiency and precision in machining processes. This versatile end mill features numerous flute-shaped cutting edges, varying from two to multiple flutes, depending on the specific requirements of the task at hand. The innovative flute design ensures swift chip removal, enhancing the overall machining speed and reducing the downtime required for clearing debris.2. Unparalleled Performance:With its unique flute design, the Flute End Mill offers unparalleled performance, delivering exceptional cutting capabilities across a wide range of materials. The tool's precisely engineered flutes provide outstanding chip evacuation, preventing chip build-up and minimizing heat generation during machining operations. Consequently, this results in enhanced tool life, reduced cutter wear, and improved surface finishes on the machined components.3. Versatility Across Industries:The versatility of the Flute End Mill makes it a sought-after tool among various industries. From aerospace to automotive, and from medical to mold and die applications, this cutting-edge instrument adapts effortlessly to the specific demands of each sector. Its ability to handle a multitude of materials, including aluminum, steel, and composites, further expands its usability, making it an invaluable asset to any manufacturing operation.4. Advancements in Design and Manufacturing:The success of the Flute End Mill can be attributed to continuous improvement in design and manufacturing techniques. By employing state-of-the-art technologies and engineering expertise, the manufacturer has achieved astounding progress, ensuring that the tool consistently delivers precise results. Ongoing research and development efforts further refine the flute geometry, materials, and coatings, enhancing the tool's durability, performance, and versatility.5. Impact on Efficiency and Productivity:The Flute End Mill has emerged as a game-changer in the manufacturing industry due to its ability to dramatically enhance efficiency and productivity. The combination of its advanced design and superior performance significantly reduces machining time, enabling manufacturers to streamline their operations and meet demanding production schedules. The tool's enhanced chip evacuation properties mitigate the risk of machine downtime caused by chip accumulation, further bolstering productivity.6. Cost Savings and Environmental Benefits:The implementation of the Flute End Mill translates into substantial cost savings for manufacturing companies. The tool's extended tool life and reduced wear lead to fewer tool replacements, thereby reducing production costs. Additionally, the efficient chip evacuation system minimizes energy consumption, contributing to a greener and more sustainable manufacturing process.7. The Company behind the Flute End Mill:Although we cannot disclose the brand name, the company revolutionizing the manufacturing industry with the Flute End Mill has a proven track record of excellence. Committed to innovation and quality, the company continues to push boundaries, developing cutting-edge solutions that address the evolving needs of modern manufacturing.Conclusion:The Flute End Mill represents a new era in precision machining, optimizing performance, productivity, and cost-effectiveness for manufacturing operations across industries. Its advanced design, coupled with the manufacturer's unwavering commitment to innovation, has solidified its reputation as an indispensable tool. As manufacturing processes continue to evolve, the Flute End Mill is poised to remain at the forefront, empowering manufacturers to achieve exceptional results in today's competitive market.